Срок службы автомобиля напрямую зависит от качества и периодичности его обслуживания. Сотни тысяч километров на одометре значат намного меньше, чем нерегулярное ТО посредственными расходниками. Одинаковые машины служат у разных хозяев по-разному: половину ресурса закладывает завод-изготовитель, а половину — собственник. Сэкономил на расходниках — сократил ресурс, здесь прямая зависимость. Однако есть системы, экономия на которых скажется мгновенно — от них зависит безопасность на дороге вообще и вероятность возникновения ДТП в частности. Речь, конечно, о тормозах.
Тормозная система — достаточно простой узел, устройство которого в общих чертах одинаково на любом автомобиле: педаль — вакуумник — ГТЦ/колдун — трубки — «тормозуха» — суппорт — колодка — диск/барабан. Особенности и дополнительные элементы — штрихи к портрету, который сути не меняет. Но изначальная простота — залог не только долгой службы, но и высоких требований к каждому элементу системы. Ту же тормозную жидкость, которая гигроскопична, нужно регулярно менять, иначе однажды, в самый нужный момент, прожать педаль уже не получится. Что уж говорить о колодках! Однако говорить надо, потому что многие автовладельцы, отмахнувшись, совершают фатальную ошибку, выбирая не оригинальную запчасть, а более дешевый аналог.
Простой пример — народная «ГАЗель−3302», запчасти на которую делает великое множество производителей. Еще бы, «железный конь», на котором едут весь отечественный малый бизнес и миллионы людей. Да и, казалось бы, что может быть такого особенно в простой колодке? Изогнутая металлическая пластина с зафиксированной на ней фрикционной накладкой. Принцип работы предельно прост: перевод кинетической энергии в тепловую.
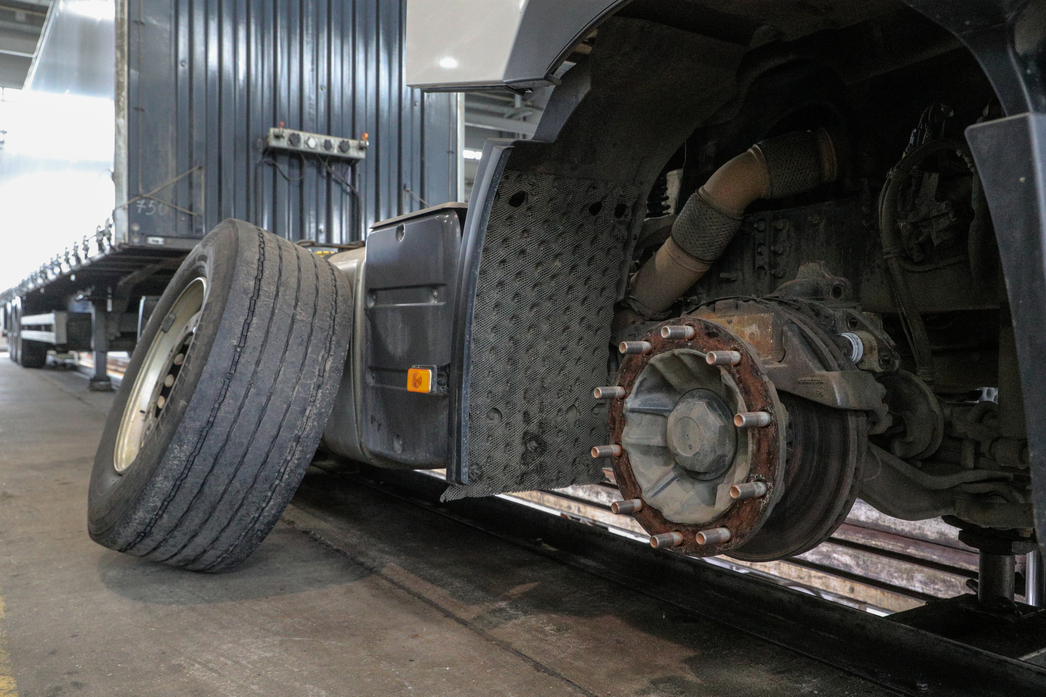
При торможении в результате правильной работы всего тормозного механизма колодка прижимается к внутренней поверхности тормозного барабана, создавая силу трения. При этом пара трения колодка-барабан нагревается до 200 °С, таким образом забирая в себя кинетическую энергию, а машина останавливается. Космических технологий в такой несложной детали не предвидится, но даже тут «смежники» и производители аналогов «выкидывают фокусы».
Надо сказать, что в России редко проводят испытания запчастей: импортные производители по умолчанию рекомендуют исключительно фирменную продукцию, не раскрывая причин, а российские предприятия будто стесняются говорить о себе. С другой стороны, тот же Горьковский автомобильный завод обладает целой собственной лабораторией, где регулярно проводят исследования не только собственных расходников и автозапчастей, но и продукции других предприятий, которые производят аналоги.
К великому сожалению, такие проверки каждый раз показывают, что в красивые коробки порой упаковывают изделия, которые произведены с чудовищными нарушениями конструкции! В руки портала «АвтоВзгляд» попали результаты испытаний заводчанами тормозных колодок стороннего производителя — к сожалению, и с этими элементами тормозной системы не удалось избежать «чудес».
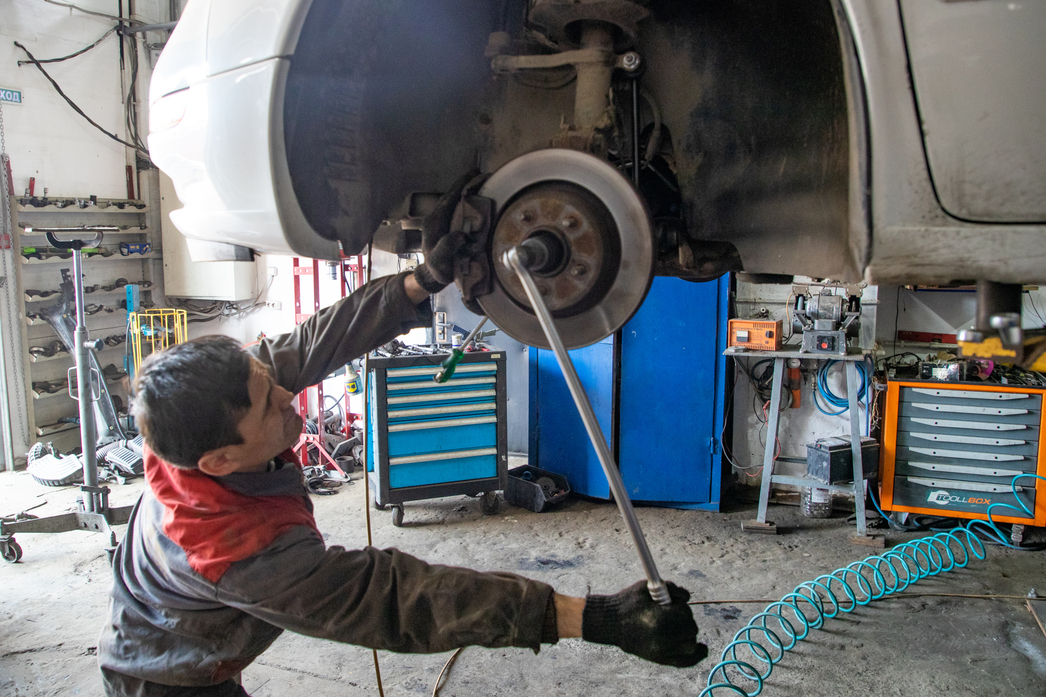
К примеру, оказалось, что проверить радиус сферы колодки попросту невозможно, по причине того, что деталь не касается роликов на специальном измерительном оборудовании. Она кривая! Не лучше дела обстоят и с толщинами металла: толщина ребра колодки составляет 4,5 мм вместо 5±0,2 мм, толщина обода — 2 мм вместо 3,5±0,2 мм — как на оригинальной детали.
Выяснились и серьезные несоответствия материалов и их обработки требованиям конструкторской документации. Так, марка стали ребра колодки — 15СП, тогда как на оригинальных деталях применяется марка Ст.25. Твердость же закаленных участков составляет менее 20HRC при требуемых 32HRC. Читайте, закалка требуемых зон фактически не производилась! Разумеется, одними замерами испытания не ограничиваются. Колодка была проверена «в деле»: на разрывной машине определялось усилие, при котором произойдет разрушение клеевого соединения между фрикционной накладкой и колодкой. Смятие кромки произошло уже при приложении нагрузки в 3000 кгс при минимальной в 3500 кгс согласно конструкторской документации.
На дворе осень, асфальт покрылся лужами и палой листвой, а в некоторых регионах уже и снег выпал. Тормозной путь вырос сам по себе, исключительно по погодным и климатическим причинам, но если еще и с тормозными механизмами «нахимичить» в погоне за извечной нашей экономией — то причина горячо сожалеть о своей недальновидности возникнет куда скорее, чем кажется. Увы, так бывает всегда.