Немецкая компания EDAG Engineering утверждает, что разработала революционный способ построения ультра-легких автомобилей, который к тому же еще и дешев. Метод EDAG сочетает в себе несколько новых технологий и прежде всего – крупномасштабную 3D-печать компонентов и использование высокопрочной, гибкой и устойчивой к атмосферным осадкам ткани в качестве материала экстерьера. Побочным эффектом применения технологий станет и резкое сокращение сроков и стоимости разработки новых моделей.
Результаты исследований были представлены в виде концепта EDAG Light Cocoon. Кузова Light Cocoon производится с помощью стереолитографии (SLA), в которой ультрафиолетовые лазеры отверждают смолы в виде ультра-тонких слоев, пока не получится запрограммированный объект. Металлические элементы конструкции также выполнены с помощью аналогичного процесса, называемого селективным лазерным спеканием (SLS), в котором вместо смолы использован порошкообразный металл.
В настоящее время технология позволяет использовать такие металлы как сталь, титан, алюминий и медь, «порошковые» детали из которых, по словам руководителя проекта Мартина Хильбрехта, обладают практически теми же характеристиками, что и при традиционных способах обработки, устойчивы к усталости металла и пригодны для сварки. В ближайшем будущем к списку материалов может добавится дешевая альтернатива карбону – армированные волокном пластмассовые детали, произведенные аналогичным способом.
Как утверждают в EDAG, использование такой технологии в автострении позволит заимствовать решения у природы, создавая прочные конструкции по образцу и подобию аналогов из мира растений и насекомых. В случае с концептом EDAG Light Cocoon, идея жесткого каркаса позаимствована у листа растений и скелета птиц.
В качестве же внешней оболочки в EDAG предлагают использовать специально разработанный высокопрочный всепогодный материал, который создавался при участии компании Jack Wolfskin, известной своей спортивно-туристической экипировкой. «Кожа» Light Cocoon подсвечивается изнутри светодиодами, позволяя владельцу машины менять окраску авто в зависимости от настроения, выбирая цветовую схему в программе на своем смартфоне.
Тканевое покрытие кажется тонким и склонным к повреждениям от ударов или рук вандалов, но в EDAG уверены, что оно не более уязвимо, чем тонкий алюминий и сталь современных машин, а кабриолеты в разы привлекательнее для хулиганствующих элементов. Кроме того, ремонт тканевого покрытия представляется делом значительно менее сложным и дорогим, нежели рихтовка и покраска металла. Тканевые панели EDAG Light Cocoon можно стирать и на шоу-каре даже имелись ярлычки с инструкциями по уходу, как и на любом предмете одежды.
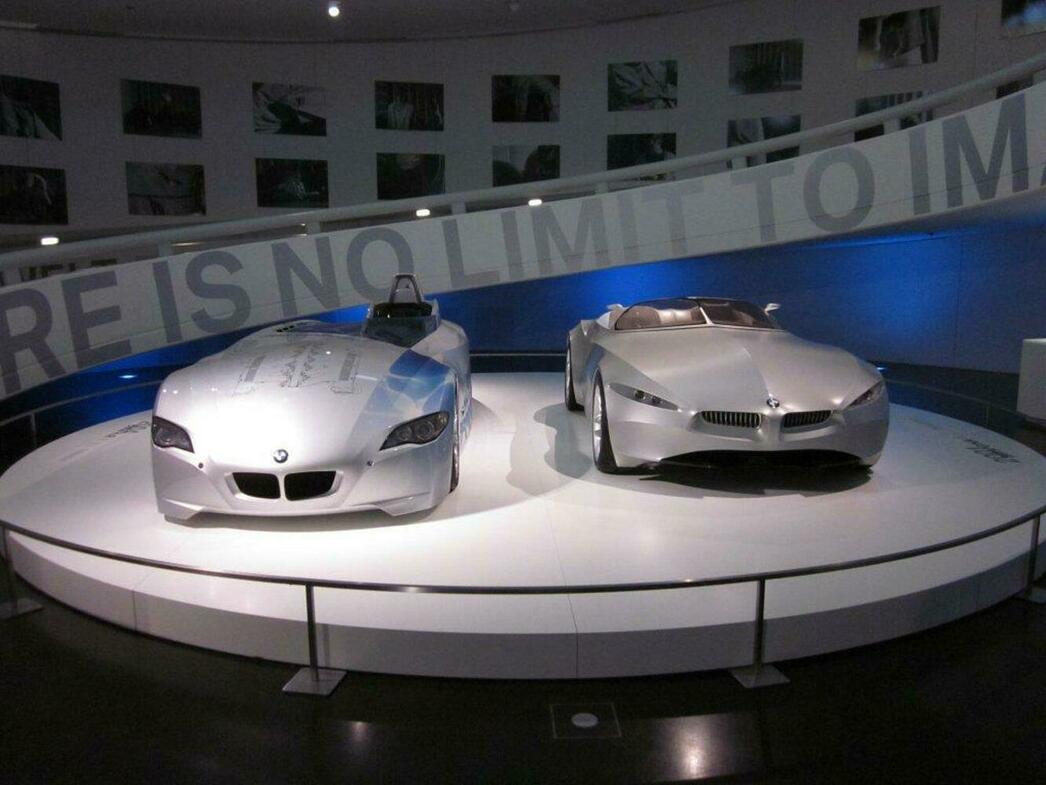
Примечательно, что подобную идею, своеобразное возвращение в начальную эру авиации, когда корпуса и несущие поверхности первых аэропланов выполняли из ткани, в нашем тысячелетии уже воплотили в виде концепта BMW GINA Light Visionary Model. Находящийся ныне в мюнхенском BMW Museum, концепт GINA Light Visionary Model был выполнен с обшитым тканью (на ощупь она похожа на очень плотный материал купальных костюмов) кузовом, форму которого водитель мог менять по своему желанию посредством системы сервоприводов и тросов.
Идея печатного автомобиля с изменяющимся кузовом из ткани кажется фантастической, но EDAG говорит, что в ее основе лежит практическое зерно и это просто вопрос времени, прежде чем технология сможет быть использована в промышленных масштабах.
– Мы смогли увеличить габаритные размеры машины с 350 мм до 650 мм всего за два года и продолжаем работать над увеличением размеров деталей получаемых с помощью 3D-печати, – заявил Хильбрехт.
По его словам, производство крупных элементов интерьера машин таким способом может стать реальностью в течение следующих пяти лет, а полностью напечатать автомобиль можно будет уже через 20 лет. Сейчас главная проблема технологии даже не размеры, а время – процесс печати одного элемента занимает несколько часов. Когда она будет решена, автопроизводители смогут радикально снизить затраты на запуск новых моделей и их производство – из процесса будет убрано громоздкое и дорогое штамповочное оборудование и обрабатывающие станки: «одна лазерная система может заменить 17-фрезерных станков с компьютерным управлением, – заявил Хильбрехт, – при том, что на перенастройку потребуются пара десятков минут – все что нужно это лишь загрузить новый файл CAD».
О том, какие просторы подобная технология открывает для китайских автопроизводителей, даже страшно подумать…